DaveL485
Staff member
Update a week early this time. I swapped my weekend with the brats to next week under request from the ex so off I toddled into the garage.
I carried on trying to put the NSF chassis rail back together, hoping i'd get that done and start taking the front part other one apart as now I have seen this subframe mount I wanna get in to the other one (I didnt get that far though). Thought i'd try and shape a plate over the whole length, as far as possible.
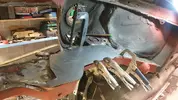
I'd already cleaned and treated this original bit which was good enough to be put back in.
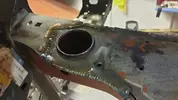
Bit of a funny shape, so I started hitting it with hammers.
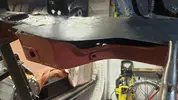
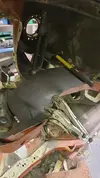
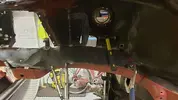
In the end I chopped the left hand side down and did it in a couple of bits.
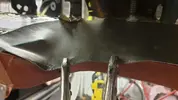
From the engine bay side
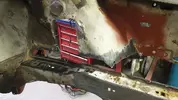
Re-attached the subframe reinforcement on the inside edge
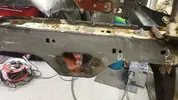
I carried on trying to put the NSF chassis rail back together, hoping i'd get that done and start taking the front part other one apart as now I have seen this subframe mount I wanna get in to the other one (I didnt get that far though). Thought i'd try and shape a plate over the whole length, as far as possible.
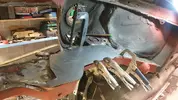
I'd already cleaned and treated this original bit which was good enough to be put back in.
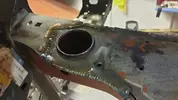
Bit of a funny shape, so I started hitting it with hammers.
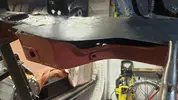
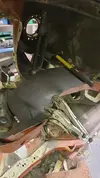
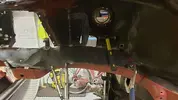
In the end I chopped the left hand side down and did it in a couple of bits.
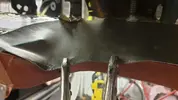
From the engine bay side
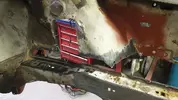
Re-attached the subframe reinforcement on the inside edge
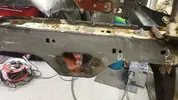