Duncan Grier
Well-Known Member
The rear line is above the bonded section as per picks below which potentially gives me some options but am fully exposed
Think spot welder 'might' reach but triple layer, plug weld or use a proper bonding glue?
Or the other lines leaving the good bit in / or not but no access to behind to help spread welds if pulled in too much bla bla bla
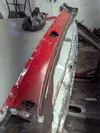
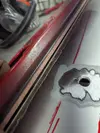
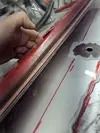
Think spot welder 'might' reach but triple layer, plug weld or use a proper bonding glue?
Or the other lines leaving the good bit in / or not but no access to behind to help spread welds if pulled in too much bla bla bla
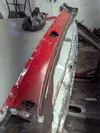
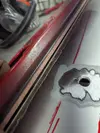
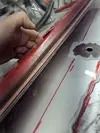