Fordy
Well-Known Member
So crank is finally in.
Assembly lube is made by Mahle and can also be used on the cam and tappets £8 for the bottle I've got total bargain and made by the same company that makes bearings
Remember to Apply lube to both lower and upper bearings and also a little on the crank journals, it breaks down into the oil so don't worry about using too much.
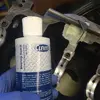
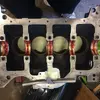
Don't forget your thrust washers need lube too
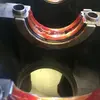
Also remember to add a bit of sealer to the dipstick tube in the block, I used loctite red gearbox flange sealer, holds gear oil fine so a little engine oil wont be a problem
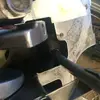
I traded my old 6 yr old Snap-on tech angle torque wrench in the other week for one of the new ones, any torque wrench will do, i just like accuracy
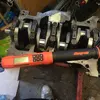
With any build... paint marks, purpose - 1 for memory that you've torqued them and 2 if you have any random failures or knocking from things undoing you see it very quickly when pulling the sump off
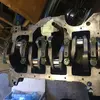
Now interestingly something I wasn't expecting, The small oil gallery plugs from Renault are undersized.
New plug 14.9mm and hole is 15mm.
Renault say press fit the aluminium plug so it expands, I've got the tool number but if its NLA or stupid price Illl lathe some bigger aluminium plugs put loctite on them and hammer them in
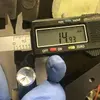
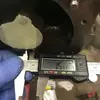
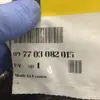
Also shimmed the new oil pump with a m6 spring washer but I might take it out and just fit 2 m6 stainless flat washers as it becomes the same size anyway's
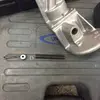
Assembly lube is made by Mahle and can also be used on the cam and tappets £8 for the bottle I've got total bargain and made by the same company that makes bearings
Remember to Apply lube to both lower and upper bearings and also a little on the crank journals, it breaks down into the oil so don't worry about using too much.
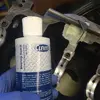
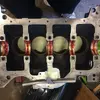
Don't forget your thrust washers need lube too
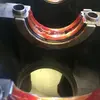
Also remember to add a bit of sealer to the dipstick tube in the block, I used loctite red gearbox flange sealer, holds gear oil fine so a little engine oil wont be a problem
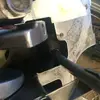
I traded my old 6 yr old Snap-on tech angle torque wrench in the other week for one of the new ones, any torque wrench will do, i just like accuracy
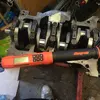
With any build... paint marks, purpose - 1 for memory that you've torqued them and 2 if you have any random failures or knocking from things undoing you see it very quickly when pulling the sump off
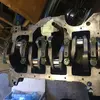
Now interestingly something I wasn't expecting, The small oil gallery plugs from Renault are undersized.
New plug 14.9mm and hole is 15mm.
Renault say press fit the aluminium plug so it expands, I've got the tool number but if its NLA or stupid price Illl lathe some bigger aluminium plugs put loctite on them and hammer them in
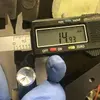
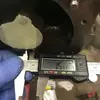
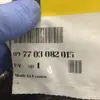
Also shimmed the new oil pump with a m6 spring washer but I might take it out and just fit 2 m6 stainless flat washers as it becomes the same size anyway's
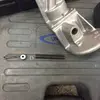