Aldo
Well-Known Member
I've been spurred on with getting the servo and pedals fitted and getting into the garage whenever I can.
I refitted the ABS pump and lines along with the brake master cylinder. Giving things a scrub as I went. I decided to paint the vac pipe bracket as it was rusty AF.... like everything else from that 172.
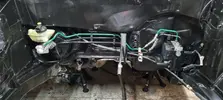
I've had the subframe sat on a bench for a couple of weeks ready to go, until I realised the inner ARB bushes were too small. So I ordered some Powerflex ones and got them fitted yesterday. Much easier doing them on a bench than on the deck! This let me get the subframe mounted to the car loosely and also means I don't need to walk around it anymore.
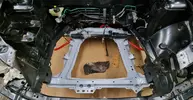
Before the engine goes in, I need to sus out a heat shield. The campus one can be used, but I'd like to extend it up round the master cylinder. I'd also like to fit the shield that goes over the rack but I'll need to make some mods to fit the 3rd fastener.
Brake pipes are another thing I need to get in before the engine. No surprises that the 172 ones were mega crusty so I've remade them from Cuni. Got three of them done last night, copying the originals. I'll need to shoot from the hip with the nearside front as it was a copper one on the 172, so nothing to copy.
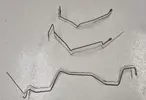
I've not confirmed it, but I'm fairly sure that from the brake line joint under the passenger footwell to the rear bracket is the same between 172/Campus. Fingers crossed, as it would save a job.
Had to order a new flaring tool as well since the one I have is SAE fitment only.
I refitted the ABS pump and lines along with the brake master cylinder. Giving things a scrub as I went. I decided to paint the vac pipe bracket as it was rusty AF.... like everything else from that 172.
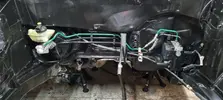
I've had the subframe sat on a bench for a couple of weeks ready to go, until I realised the inner ARB bushes were too small. So I ordered some Powerflex ones and got them fitted yesterday. Much easier doing them on a bench than on the deck! This let me get the subframe mounted to the car loosely and also means I don't need to walk around it anymore.
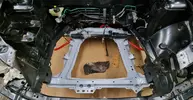
Before the engine goes in, I need to sus out a heat shield. The campus one can be used, but I'd like to extend it up round the master cylinder. I'd also like to fit the shield that goes over the rack but I'll need to make some mods to fit the 3rd fastener.
Brake pipes are another thing I need to get in before the engine. No surprises that the 172 ones were mega crusty so I've remade them from Cuni. Got three of them done last night, copying the originals. I'll need to shoot from the hip with the nearside front as it was a copper one on the 172, so nothing to copy.
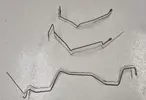
I've not confirmed it, but I'm fairly sure that from the brake line joint under the passenger footwell to the rear bracket is the same between 172/Campus. Fingers crossed, as it would save a job.
Had to order a new flaring tool as well since the one I have is SAE fitment only.