From Martin F:
Hi Andrew,
Great that you are tackling this well done. It's not rocket science, so should work out well.
Some points I would raise:
1. Loom interconnects, bulkhead connectors - great adds flexibility and ease of maintenance, but reduces reliability significantly, even military conectors, they are one of your highest failure points, I do this sh_it for living, and we are always looking to eliminate them. So I would say, if you can avoid the bulk head connector, simply do... you are not going to be pulling the loom, replacing the engine more than once, max twice in the vehicle's lifetime.. certainly not on a frequent basis. The "connectorisation" if you like, assists faster cheaper install for the manufacturer, it doesn't add technically to the quality, just convenience. Keep it simple if you can, but I do understand allows additional wires to be run in later, but you could make provision for that now with planning.
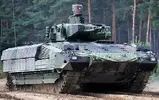
RM1438623505.jpg (14.28 Ki

Viewed 240 times
So I know a thing or two, lets say two, of military connectors, harsh environments, and reliability data...
2. Single bulkhead feedthrou connection will defeat your attempts at signal integrity, screening effectiveness, and signal type isolation that you had with your cable screens to that point in the loom- you have no choice than carry your screen through on a pin... your screen at that point is defeated... not techno ballshot, just plain fact. The only solution as we do, is to use guard rings round sensitive signals, and that takes up a large number of pins on your multiway...
3. Have a look at the automotive -55 +125 deg C Molex to name one, excellent product for power, signal, and wire to wire interconnects... the automotive manufacturers have done more work than anybody on suitable and sufficient product to meet high reliability and lower cost... all cable harness reliability studies with real field significant data are automotive...
4. If I understand right, you are thinking of keeping the OE variable reluctance tdc sensor, and presume trigered off the OE flywheel tooth pattern? All good, just remember, you will then need the cam sensor to identify tdc no.1 for ignition as well. But should be easy, as the cut-outs are already in some versions of the cam sprockets, come in through the front timing case cover.
5. Controlling the Amal valve is one option (I think it's 3 wire from memory, could easily be wrong though), or there are cost effective, and reliable single ended solenoids you could just control from a pwm output.
6. IMHO I wouldn't sweat a bunch over (semi) sequential over batch injection fire necessarily, we're not F1 here, and the 12V PRV isn't the most lean burn engine by far, so not a huge amount to gain in reality, semi is nice to have, but wouldn't add the cam sensor to get that, only really so that you can go coil packs and lose the dizzy.
7. IMO I would go high impedance injectors, and save the need for the higher current peak and hold injector drivers.. yes we could argue the relative merits of this and that, but modern multi-spray injectors.. whack 'em in...
Biggest thing though, as already comes through in your post - enjoy it, it should be a fun project full of discovery. Great go for it, keep us posted as Vince says
Martin