Got out there this morning bright and breezy! and started making the patch for the bumper support. I had a good look at the piece I cut out and noticed a curved edge on the bottom!
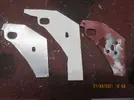
Starting to form the curved edge! and the curved hole.
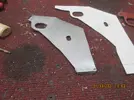
The plan is to drop a bit of weld in that bottom corner and form the curve with the grinder!
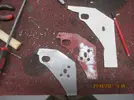
So, got it cleaned up and painted the back of it with zinc primer and left it to dry. I spotted another perforated section in the inner arch that needs looking at!
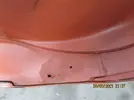
This is paper thin, gonna cut it out! Card board!!!!!
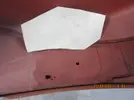
I then cut a plate, and gave it a bit of a bend!
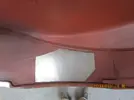
It seems to sit ok, so I marked around it and cut it out! again had to dill out a spot weld which attaches the two pieces of inner arch together.
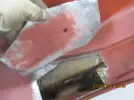
I gave the inner piece a clean and rust treatment and painted the back of the patch. Then went back to the bumper support as the paint is now dry!
After a bit of fettling, it fits quite nicely!
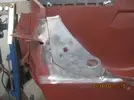
I had to mess about with the curved bit at the front but got there in the end!
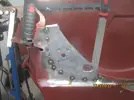
I then went to the curved edge that I mentioned earlier and dropped some weld on it and ground it down!
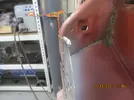
It doesn't look too bad at all!
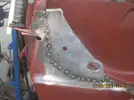
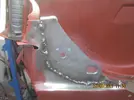
I managed to get some weld on the other curved section without blowing the arse out of it - result!
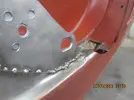
I then decided to turn the car up on its side so that I am welding down on to the metal! Had a couple of blow outs, but nothing major.
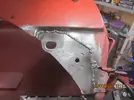
I then gave it a grind!
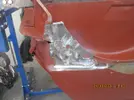
Not too shabby at all!!

Then back to the inner wheel arch.....
Paint dry
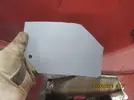
Started to tack it into position..
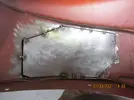
Had some issues with this one! some rather large gaps....point to note... next time just make a new patch, you will save a lot of hassle and time!! Also, don't leave your favourite bodging tool on the car and start hammering with a big hole in the inner arch as you will lose said tool down the bloody hole!! It is now residing somewhere in the roof section and won't come out!!
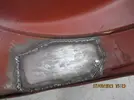
Got it welded in!! nightmare! I then got the grinder on it!

I took a look at the front of the arch and some rust there!
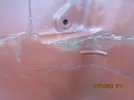
I marked and piloted the spot welds in the strap!
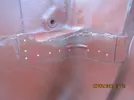
And then cut along the black line and removed the section of strap!
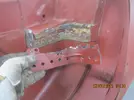
I gave the area a clean up
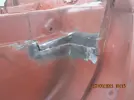
I then made a patch to replace the rusted out section of inner wheel arch!
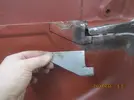
And then marked and cut it out
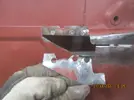
Then noticed that the boot floor skin was rusty and paper thin! some actually came off in my hand!
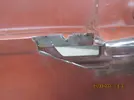
I cut the rest of it off and got an off cut to make a small patch. I used a welding magnet to hold it in position whilst I got a tack on it.
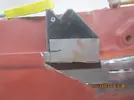
I left it long on purpose. I fettled it a bit and then tacked the one end.
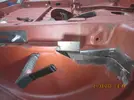
I then decided to weld along the back first, then along the front, so that I could grind the front edge of it and round it off a bit!
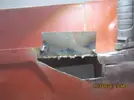
Got the grinder on it!
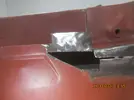
I then got a straight edge and marked the patch and cut it off!
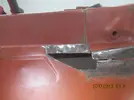
I wasn't happy with the original patch, so I made a new one, this one is much better, again I left it long!
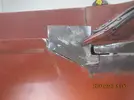
I got some zinc primer on both sections and called it a night!
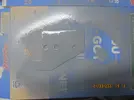
Thanks for reading guys!