Steve Swan
Well-Known Member
Electricity and water in the same place and time is bad, mkay...
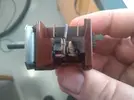
The bits arrived, it's back together and I'm reinstated as chief cook and bottlewasher
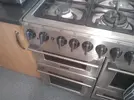
Should have left it broken.......
The other Alp axle has gone to be cleaned, and I have been on a double secret job to adapt a BMW M3 gearbox to a one piece prop, I'm not writing this up as, I'm not convinced it will actually work. There is enough rubbish on this thread already!! However I did go to the bodyshop to have a look at @paule78 's 8 to see how its going, so you need to tune in to the other side...
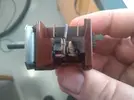
The bits arrived, it's back together and I'm reinstated as chief cook and bottlewasher
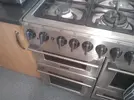
Should have left it broken.......
The other Alp axle has gone to be cleaned, and I have been on a double secret job to adapt a BMW M3 gearbox to a one piece prop, I'm not writing this up as, I'm not convinced it will actually work. There is enough rubbish on this thread already!! However I did go to the bodyshop to have a look at @paule78 's 8 to see how its going, so you need to tune in to the other side...