Right Here goes.
It is difficult to get a clear picture in your mind in reference to what your car does geometrically in a corner. Photographs from the Racetrack can be very helpful, but there is no substitute for actual measurement. I actually built a half sized string computer from Alan Staniforths Race and Rallycar handbook. It was to see what (if any) improvements could be made by playing with any of the inboard pickups. This was partly academic as being a crossmember type there is not much scope for movement. What it revealed was that nothing much could be gained by moving these pickup points around, but it also showed that the suspension produced a small increase in negative camber on bump and reduced it on droop. string experiments on moving the bottom arm down in or out only gave negative results (wrong camber changes and terrible scrub which is actual track change and is to be avoided if at all possible). Answer is to leave as it is
My Dauph has a custom Titan rack in it as I needed a quickrack. This has the same length rack bar and travel as original, but has a different body requiring different mounts. Having learnt the hard way with the 8G which also had a Titan rack, I took the opportunity to machine the R8/10 crossmember mountings to allow some adjustment before welding it into the shell. I hoped it would be enough, looks like I am Wrong yet again!!!
Back to the subject: What we need to do by adjustment is to harmonise the arcs of the upper and lower wishbones and the steering arm to give the required results, namely a slight increase in negative camber on compression, a slight reduction in Neggy. on droop, with preferably no change in steering angle if achievable. I had a mystery issue with my 8G which was that it was very nervous on undulating surfaces which was traced to 20mm of bump steer. It took an age to sort and I had to make some tools to achieve it, but I was triumphant in the end, and best of all the handling was very nice no nervousness at all, but mega turn in if required.
Pictures time again this sequence shows the gear being attached to the front wheel this allows simultaneous measurement of camber change and steering angle change. The only other special tool is the floormop which is used to jam the brake pedal on so the front wheel cannot rotate during measurement.
Pic 1 shows the scaleboard fitted to the wheel with the spirit level showing it is level (there is a centre pin on the board which is lined up with the centre of the hub dustcap)
pic 2 Shows the camber gauge on the scaleboard (an electronic protractor which must be zeroed against a known vertical surface) This is why your workshop floor needs to be level
Pic 3 Shows The whole shabang set up on rideheight and zeroed on all axis (the pointer an old R12 pushrod carries the weight of the gauge and makes it compensate for camber thrust) leaving the clock gauge spring to measure the change in steering angle only)
Pic 4 shows the front end on 2 inches of compression
Pic 5 shows it on 2 inches of droop
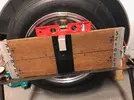
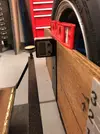
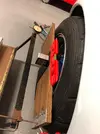
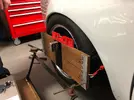
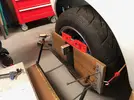