UPDATE:
Out came the dremel again and it was time to tackle the exhaust ports. They were terrible to start with, pitted, flash marks down the sides, big ridges where the valve seats met the casting. I intended to smooth all of this and blend the bowels. I didn't make the ports bigger as this would have reduced the exiting gas velocity which in theory will give more turbo lag.
To prevent me hitting the valve seats with the dremel I covered them in blue tac, this worked incredibly well and the seats came out unscaved.
Many people grind the valve guides flush with the bowel, however I didn't do this in this case due to the exhaust gas temps which could potentially melt the valve stems. I will grind them flush on the inlet ports due to the low temps.
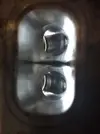
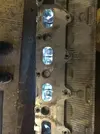
Done quite a few things over the last week or so.
First off was a 36K service of the car, this included new plugs, oil, cabin filter, oil filter and brake fluid. Wow what a difference the plugs make, the car feels alive again and pulls so much harder.
While the car was up on the jacks i thought it was about time to replace my rear brake callipers, I had some refurbed ones spare and so now i finally have red calipers front and rear. Next month Ill replace the rear and front discs and fit braided lines.
They look much better, just never got time to doing my own as Im always busy refurbing everyone elses callipers
With the car done it was now time to carry on with its new engine

This time it was time to port the inlet ports. These were far easier the work with than the exhaust ports at the were a lot wider and shallower. I will also get most gains from re shaping and smoothing the inlet ports.
Below is an image of the ports before porting. As you can the see the partition it fairly large and will cause quite a bit of drag on the flowing air. Like the exhaust ports the walls of the port are really rough with cast marks running down the edges. The valve guides are protruding out which is also an area which will cause excess drag on the air flowing round them. My porting attempts will resolve these issues with the stock ports.
After the first pass with the 60 grit wheel the majority of the shaping is done, the partition has been knife edged to reduce the coefficient of drag on the incoming air. The ridge or hump at the start of the port has also been flattened and blended into the surroundings. The machined channels have also been blended into a smooth curve to aid air flow. The 60 grit wheel has also done a good job at removing all cast marks.
The next stages was a pass with a 120 grit wheel to further refine the contours and smooth the surface. I then used a scotch bright wheel of 180 grit and then 280 grit to smooth the surface to exceptional finish.
I have left the short radius rough (Cant see this in this view) to cause a tumbling effect on the air to increase velocity around the bend into the valve opening. This turbulence should also help with fuel atomization creating a more efficient burn.
The valve guides have been ground flush with the bowls to also aid air flow. This can be done on the inlet due to the reduced temperatures compared with the exhaust ports where the guides are left untouched to protect the valve stem from the intense heat.
I hope you guys are enjoying this build thread!!
Next time Ill blend the valve bowls and get the head skimmed then its time to install the new shiny valves
Another week and some more work done to the engine.
First off was tackling the inlet bowls. I had to get these all exactly the same to keep airflow through all the ports uniformed. I therefore like before put blue tac around each valve seat to protect them should i slip. I then went in again with the 60 grit wheel then 120. I tried to time myself on each port to prevent me over grinding one of the bowls. After this stage I used a 240 grit flapper wheel to further smooth the contours of the bowl.
Before finsishing with the buffing wheels I inspected the bowls with a vernier calliper, they were all within 0.25mm of each other which I don't think is to bad for just a dremel.
Finally using the finishing buffs I finished the bowls in 400 grit as I want low air resistance just before entering the chamber.
Now with the porting and polishing complete (THANK GOD!!!) its time to get the head cleaned up and skimmed ready for painting. To achieve this i will sand blast the exterior of the head. This means I have to mask off all the machined surfaces and bolts holes. For the combustion chambers I made a aluminum plate to block off this area. Using the head gasket as a template I marked out the bolts holes and drilled them out. Then using 120mm long M10 bolts and nuts I bolted the plate on to the head using the existing head bolt holes (I hope this makes sense

)
Over the weekend Ill mask off the other areas using a mix of electrical tape and duct tape. Then I can get it blasted on monday.
I now have to decide the colour scheme of the engine. I was thinking of a gun metal grey for the head and rocker cover with a black intake port and block.
Any ideas will be greatly welcome.
Cheers
Not a huge amount done this weekend.
Saturday I picked up some forged rods from @
shakey_hand_man, had the pleasure of looking over his clio and my god its a sight to behold. If mines half as good as that ill be happy.
Right back onto the engine re-build I reassembled the top end of the engine and masked all the machined surfaces off with special tape. This will allow me to blast the exterior giving me a good surface ready for paint. Ill do this tomorrow at work then I should be able to remove the tape and wash the head in hot soapy water to remove any foreign particles. Then ready for paint and reassembly.
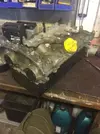