Chris74#
Well-Known Member
So, the 5 is currently with Mike Dullforce, so I took the opportunity to get the Clio in the garage so that I can get the welding done for the MOT. Just needs the front jacking points sorting.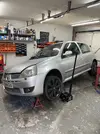
I must admit that there is something about this car, I drove it back from the garage where it has been living and it was so much fun! Lots of power and the sounds and smells are great!
The front jacking points are shot and failed on the MOT so that is the job for this weekend.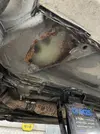
I decided to use the old jacking pints from the 5 and got to work cutting the rust out of these points. I then cut the 5 jacking point to suit and after giving it all a good soaking of rust eater I welded the piece in position. I then ground the welds down and went round it with seam sealer!
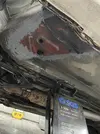
Then I got some epoxy paint mixed up and gave it all a liberal coating of the stuff! I then got the bracket that I powder coated previously and fitted that after cleaning up the bolts!

That'll do for now, its solid and sealed. I'll squirt some waxoyl in there tomorrow after I have finished the other side!
Thanks for reading guys!
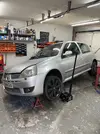
I must admit that there is something about this car, I drove it back from the garage where it has been living and it was so much fun! Lots of power and the sounds and smells are great!
The front jacking points are shot and failed on the MOT so that is the job for this weekend.
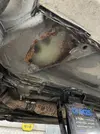
I decided to use the old jacking pints from the 5 and got to work cutting the rust out of these points. I then cut the 5 jacking point to suit and after giving it all a good soaking of rust eater I welded the piece in position. I then ground the welds down and went round it with seam sealer!
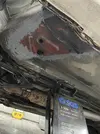
Then I got some epoxy paint mixed up and gave it all a liberal coating of the stuff! I then got the bracket that I powder coated previously and fitted that after cleaning up the bolts!

That'll do for now, its solid and sealed. I'll squirt some waxoyl in there tomorrow after I have finished the other side!
Thanks for reading guys!