Now the sills are on, I decided it was time to tackle the area that has been on my mind from the start, the fuel flap. I'm unsure exactly why this area was worrying me, it doesn't even look that bad. Maybe it was because it was an awkward shape, or that it was so on-show, I'm not sure. Regardless, it was time to put on my big boy pants and get on!
Here's the offending section.
Going back a few months now, after deliberating for waaay too long, I decided it was impractical/beyond my capability to repair (foreshadow). I therefore looked to buy a section from another car. After asking around, it seemed like £50 was the going rate. Being such a small section that I wanted to take from the panel (and that I don't like parting with money), This just wouldn't do. I've always done stuff myself and hate having to pay money out or ask for help. I'll just figure out how to repair it (foreshadow). At the last minute, I found a guy who was willing to part with one for £35. Bargain i thought! (foreshadow) I paid the man via Paypal family & friends (foreshadow)......I'm sure you can guess where this is going. I waited for it to arrive.......and waited......and waited! After a bit of back and forth, it was clear the part wasn't coming.
(For the record, I do actually believe the guy was genuine. He sent me photos and proof of postage. It's just that royal mail are shocking.)
Regardless, the moral of my story is -
If you want something doing, do it yourself!!
After a bit of paint/rust removal, this is what I'm faced with.
As I didn't have enough of the original shape to work with, I needed to make a template. Nabbing a photo of an in-tact section from
@Chris74# thread (thanks Chris, I hope you don't mind), I imported it in to Solidworks. I took a reference measurement from what was left of my panel and scaled the picture to suit. I then sketched around the shapes and dimensioned everything. I also used the hole centres on my fuel flap hinge to double check the scale.
Drop that on a drawing and save off as a DXF.
Imported the DXF in to
Cricut design space.
Card template cut on the
Cricut.
I then decided I needed an orientation reference mark. The
Cricut has the facility to draw too, so it was pretty easy to add the required marks.
Test fit on the flap looks good.
Test fit on the panel and align with what's left of the cutouts.
Mark the reference lines and around the outside.
Cut and remove the outer skin.
Mark and cut out the repair section
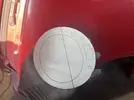
Test fit in place.
Now to deal with the section that comes up the side wall.
I've left the tab long to be trimmed off afterwards.
Tacked in place
I then built the weld up to add enough material to create the radius at the bottom of the small repair section I added earlier.
First grind back
A few rounds of weld, grind, weld, grind.
Chain drilled and slit the holes out.
Cleaned up with a combination of dremel, band file and hand files.
Lick of primer on the outside and hydrate on the back side.
The back side aint gonna win any beauty contests. But how many of our backsides are? lol
A quick before and after
And she's done!
Sorry for the LONG post! hopefully you found it interesting or potentially useful. It was a long winded, fiddly approach that might well fall off the first time I go over a bump. But I'm glad I did it and it certainly isn't any worse than if I'd have put a patch in from another car.
In summary, fuck 'em, do it yourself
