Update - We finally have a roof and a drive
Boarded the roof last Wednesday with osb3, took a day easy work with the paslode first fix nail gun i borrowed for the job. We then sheeted the roof up with 1000ga to keep the osb dry.
The next step was lay the grp covering. You might ask why grp over mineral felt ? the main reason being longer lifespan and i can lay it myself without paying anybody as i do not have any gear to felt a roof.
The only downside to Grp is you need temperatures above 5deg and dry weather to lay, middle of winter far from ideal to be honest. However with the dry spell we have had recently i decided to go for it.
Went around a few places locally to get some quotes on materials - prices were from £700-900. I done a bit of digging online and found a good deal with cfs fibreglass supplies. Came in about £700 with all the tools and ample gear to complete the job.
Started last Sat, spent a day fitting the edge trims/drip and bandaging the joints on the osb. Sunday layed the resin/ 600ga matting 6 hours for me and
@Sheryl_O to do 46sqm, this stage is called laminating. Weather was nice, around 8 deg and sun was out so the grp went off superb with winter catalyst, I found it fairly easy to do due to using fibreglass matting in the past. Basically all you do is cut the matting to length - wet out the board with resin using a roller, then lay down the matting and wet out the top with more resin. Next use a consolidator roller on top to remove air and fully wet out the matting. Precision is required when mixing the resin - the correct ratio and mixing of grp to the catalyst (hardener) is needed - I was using winter catalyst at 4%. No pics of these stages as its horrible sticky stuff that gets everywhere
As the weather played ball the resin set very well before running out of light. The roof feels solid with 600ga matting could probably park a car on it lol. Usually most kits supply 450ga matting which is intended for occasional foot traffic and 600ga is for balconies etc.
With grp you have 2 stages laminate and top coat, From what i gather the top coat is a gel coat which gives uv protection and additional water resistance. Ideally the top coat needs to be applied within 24hours of laminating before the resin is fully cured. As the roof is big and the daylight hours are short we had to do this after 24hours which involved sanding the roof with 40 grit sandpaper to key up and wipe down with acetone to ensure a good bond.
We started top coating on Tuesday as the weather was fair However the temperature was all over the place. The top coat is funny stuff basically like treacle and takes a bit of effort to apply. The sun was out mixed up the first 4kg with 4% catalyst which went off far too fast giving about 15mins working time out of the bucket before going off so wasted a fair bit sadly. After this i altered the catalyst ratio to 3% to give a longer working time as materials were tight.
Done 3/4 of the top coat and then had issues at this point - we had 1x 20kg tin & 2x 5kg tins. At this point i had used the 20kg tin and 1x 5kg tin which all seemed to be going off fine. Mixed up the last tin to work back towards the ladder roughly 5sqm, applied it and the top coat did not seem to go off properly just tacky, still not sure if this was down to slight drop in temperature or duff top coat? Anyway it eventually went off fully about 24hours later, i feared that i would need to wipe down and re apply but it seems to have set just fine with no problems, luckily did not rain in this period !
Still got the front and side trim to coat as i ran out of daylight and had to order anther 5kg of top coat and it has pissed down the last 3 days. Its totally watertight so the last bits are just cosmetic, hopefully get a nice dry day soon so can get it finished off. Drive needs blasting down and sealing the lads are coming back in the new year to do this again need a nice dry day.
Next step render the front and doors on

slowly getting there
A few pics
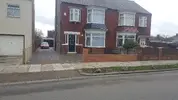